电容储能点焊机点焊的缺陷有哪些?
来源:http://www.tayfsk.com/ 发布时间:2023-09-11 浏览次数:0
电容储能点焊机点焊的焊点如果质量良好,无论从外观还是从焊核内部都是没有缺陷的。从外观看,焊点是表面平整,无烧伤、压痕深等各种缺陷。从内部看,应有尺寸合适的焊核,焊核应是很致密的铸造组织,核内不能有缩孔、疏松、裂纹等缺陷。
If the quality of the spot welded joints of the capacitor energy storage spot welding machine is good, there are no defects in both the appearance and the interior of the weld core. From the outside, the solder joint has a flat surface and no defects such as burns or deep indentations. From an internal perspective, there should be a properly sized weld nugget, which should be a very dense casting structure and free from defects such as shrinkage, porosity, and cracks.
电容储能点焊机如果在点焊时,焊件清理不好,规范选择不当,都能引起缺陷的产生。点焊的缺陷主要有:
Capacitor energy storage spot welding machines can cause defects if the welding parts are not cleaned properly and the specifications are not selected properly during spot welding. The main defects of spot welding are:
1.未熔透:
1. Incomplete penetration:
未熔透即在点焊时,没有形成“扁豆”样的铸造点焊组织。这种缺陷危险。它会大大降低焊点的强度。而且这种缺陷一般不能从外观上检查出来。储能点焊机产生未熔透的主要原因是由于焊接电流密度太小或焊接时间短使焊接部位加热不足所造成的。造成焊接部位电流减小的原因是多种多样的。
Lack of penetration refers to the lack of formation of a "lentil" like cast spot welding structure during spot welding. This defect is dangerous. It will greatly reduce the strength of the solder joint. Moreover, such defects are generally not detectable from the appearance. The main reason for incomplete fusion in energy storage spot welding machines is due to insufficient heating of the welding area due to low welding current density or short welding time. There are various reasons for the decrease in current at the welding site.
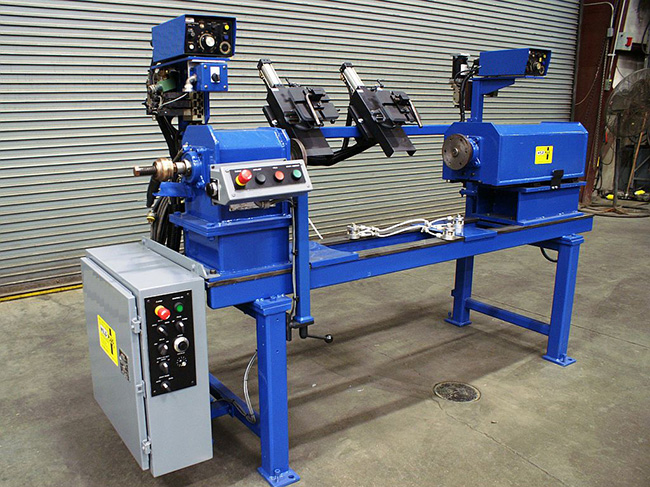
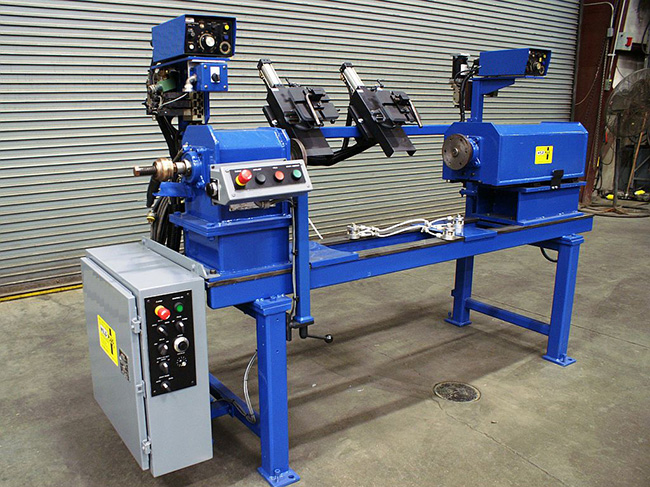
如:①焊接工艺规范调节不合适,②二次回路电阻增大,③有部分分流现象,④网络电压下降等。
For example, ① improper adjustment of welding process specifications, ② increase in secondary circuit resistance, ③ partial shunt phenomenon, ④ decrease in network voltage, etc.
2.飞溅:
2. Splash:
飞溅在储能点焊机中经长出现。少许的飞浅是不可避免的,如果飞溅太大,会造成压痕过深。工作表面的凹陷太深,会造成焊核强度明显下降。飞溅有两种,即初期飞溅和末期飞溅。初期飞溅是电流闭合瞬间产生的。其主要原因是由于予压时间太短或焊件表面不清洁及压力小所造成的。储能点焊机末期飞溅是在通电末期产生的,其原因主要是焊接电流太大或焊接时间太长,核内熔化的金属大到周围塑性环在电压力下已经包不住了,而造成液体金属的外溢。
Splash appears in the energy storage spot welding machine for a long time. A slight splash is inevitable, and if the splash is too large, it can cause excessive indentation. If the depression on the working surface is too deep, it will cause a significant decrease in the strength of the weld nuggets. There are two types of splashes, namely early splashes and late splashes. The initial splash is generated at the moment of current closure. The main reason for this is due to the short pre pressing time, unclean surface of the welded part, and low pressure. The final splashing of energy storage spot welding machines occurs at the end of the power cycle. The main reason is that the welding current is too high or the welding time is too long, and the molten metal in the core is so large that the surrounding plastic ring cannot wrap it under electrical pressure, resulting in the overflow of liquid metal.
飞溅的办法是查找产生飞溅的原因,适当地调节焊接规范或改善工件表面质量。
The method to eliminate splashing is to identify the cause of splashing, adjust welding specifications appropriately, or improve the surface quality of the workpiece.
上一篇:激光焊接系统在化工领域的使用
下一篇:焊锡丝的自动焊接与人工焊接的区别